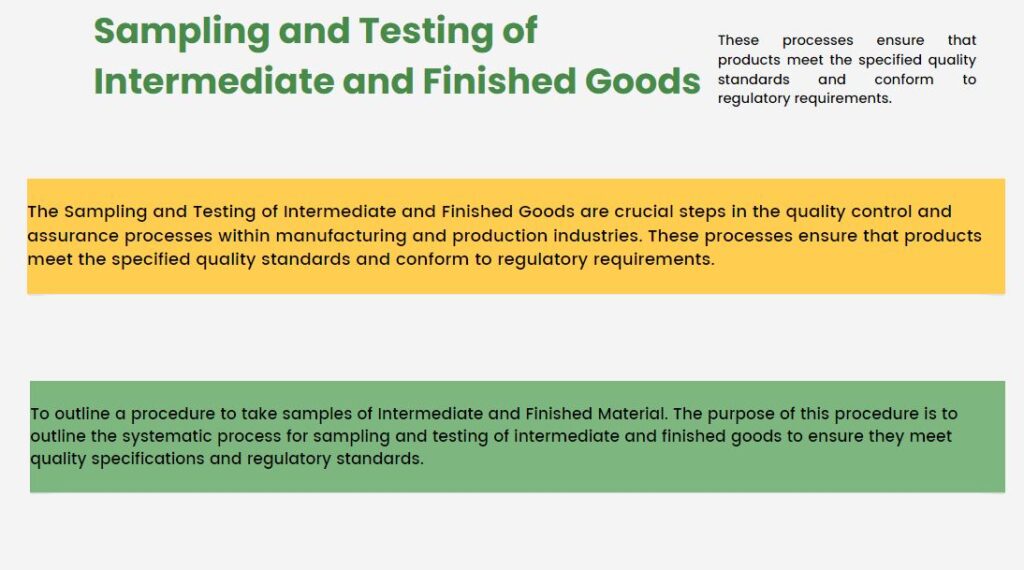
The Sampling and Testing of Intermediate and Finished Goods are crucial steps in the quality control and assurance processes within manufacturing and production industries. These processes ensure that products meet the specified quality standards and conform to regulatory requirements.
PURPOSE
To outline a procedure to take samples of Intermediate and Finished Material. The purpose of this procedure is to outline the systematic process for sampling and testing of intermediate and finished goods to ensure they meet quality specifications and regulatory standards.
SCOPE:
This SOP applies to sampling of intermediate materials and Finished Materials.
RESPONSIBILITIES:
Production Incharge, QC Incharge and QC Analyst are responsible for representative sampling according to recommended plan.
- Quality Control (QC) Team: Responsible for sampling and testing procedures.
- Production Team: Responsible for providing samples and facilitating testing.
- Quality Assurance (QA) Team: Overseeing compliance with quality standards and regulatory requirements.
INTRODUCTION:
The Q.C. department tests all the intermediate products during process and Finished Goods.
SIGNIFICANCE:
Samples are drawn for testing of materials according to standard specification for the manufacture of quality / standard product representing the whole lot.
SAMPLING TOOLS
- Containers opener
- Gloves
- Poly bags.
- Balances
- Forceps
- Scissors
- Spoons
- Scopes
- Pointed long/sharp headed spoon
- Rubber bands
- Marker
- Cutters
PROCEDURE Sampling and Testing of Intermediate and Finished Goods
SAMPLING OF INTERMEDIATES PRODUCTS.
Intermediate products are those products, which are being passed through the process of manufacturing. They are not finished products e.g. dried granules, premix granules, final mixed granules, compressed tablets, coating of tablets etc.
Dried granules are sampled after drying of wet granules by Q.C. inspector.
On information through “Request for Sampling” samples are drawn, recorded in “Register”. Take samples from each dried pan from upper, middle and lower portions. Tighten poly bags immediately otherwise granules, observed during analysis, may absorb moisture.
Final mix granules, compressed tablets, cores, coated tablets of different types are sampled by Q.C. inspectors in poly bags with the help of spoon. Avoid touching of fingers with the products.
Blister strips, packing cartons etc are sampled according to testing requirements.
Production Pharmacist sends request for analysis in duplicate. Q.C. Analyst takes sample according to specification. After analysis as per standard analytical procedure and specifications, results are noted in ‘Analytical Record for Intermediates and Finished Goods’. The store is placed in quarantine till “RELEASED” or “REJECTED” verdict on the lower portion of request is received from Q.C. In case of any non-conformity, ‘Adjust’ slip is issued to production to rework for adjustment of the product to make it conformed. After clearance, the store is allowed to process further. In case of “rejection” the store is reprocessed accordingly.
If the component is failed as per specification even after rectification, these are identified as rejected and collected in a container labelled with label marked “Rejected” and placed in specified area. .Q.C Manager is responsible for approval of rectification/adjustment of process proposed by analyst while store incharge and Q.A.I are responsible to destroy the rejected materials / products on approval from M.D.
SAMPLING OF FINISHED GOODS. Sampling and Testing of Intermediate and Finished Goods
Finished Goods store in-charge/Production Pharmacist sends request for analysis to Q.C. Department. Also Q.C. is informed to take reference samples for keeping in laboratory and samples of finished
product for analysis. Q.C. Analyst takes sample according to requirement and put slip of “SAMPLED” on every batch. Q.C. Analyst takes sample according to specification. After analysis as per standard analytical procedure and specifications, results are noted in ‘Analytical Record for Intermediates and Finished Goods’. After analysis and acceptance “RELEASED” label is pasted on the batch and transfer the batch to released area by Finish Goods Store in-charge on ‘Delivery Slip’ . Store is placed under appropriate conditions of temperature and humidity and the inventory is prepared by Finished Goods Store in-charge.
In case of rejection, production and quality control department investigate/resolve the problem jointly.
Related documents
- Reference Register for Intermediate and Finished Products
- Label “QUARANTINE”
- Label “SAMPLED”
- Label “RELEASED”
- Label “REJECTED”
- Label “ ADJUST”
- Request for analysis
- Delivery Slip
- Sampling and Testing of Intermediate and Finished Goods